Le tokamak JT-60SA, a été conçu, financé et construit par l’Europe et le Japon sur le site de Naka (Japon), avec une importante contribution française, dans le cadre de l’accord « approche élargie » lancée en parallèle des accords pour la signature du site ITER à Cadarache. Depuis 2021, le CEA a pris la responsabilité des activités de R&D pour les composants de première paroi les plus sollicités : les éléments du divertor de ce tokamak supraconducteur, le plus grand jamais construit avant ITER.
La CEA a été un acteur majeur dans la construction de cette machine de fusion japonaise, fournissant la moitié du système magnétique supraconducteur toroïdal, l’usine cryogénique et des alimentations électriques. JT-60SA a pour objectif d’être une machine en support de l’exploitation d’ITER et de contribuer aux recherches pour la conception d’une future centrale à fusion. Les composants de première paroi faisant face au plasma font partis des éléments clés des tokamaks. JT-60SA commencera ses expériences avec un divertor constitué d’un assemblage graphite sur un alliage de molybdène (TZM) pour ensuite évoluer vers une technologie à base de tungstène.
En 2021, le CEA a pris la responsabilité des activités de R&D réalisées dans le cadre du consortium EUROFusion pour les éléments du divertor de JT-60SA. A ce titre, Marianne Richou, scientifique spécialiste des matériaux au CEA-IRFM et Adjointe au Chef de Projet du Work Package Divertor d’EUDROfusion, est en charge des activités divertor pour JT-60SA. Côté CEA, les chercheurs concentrent dans un premier temps leurs efforts sur la validation de la conception (calculs électro magnétique et thermomécanique) et la qualification (tests non-destructifs, tests à hauts flux thermiques sur la plateforme HADES) des éléments du premier divertor en graphite.
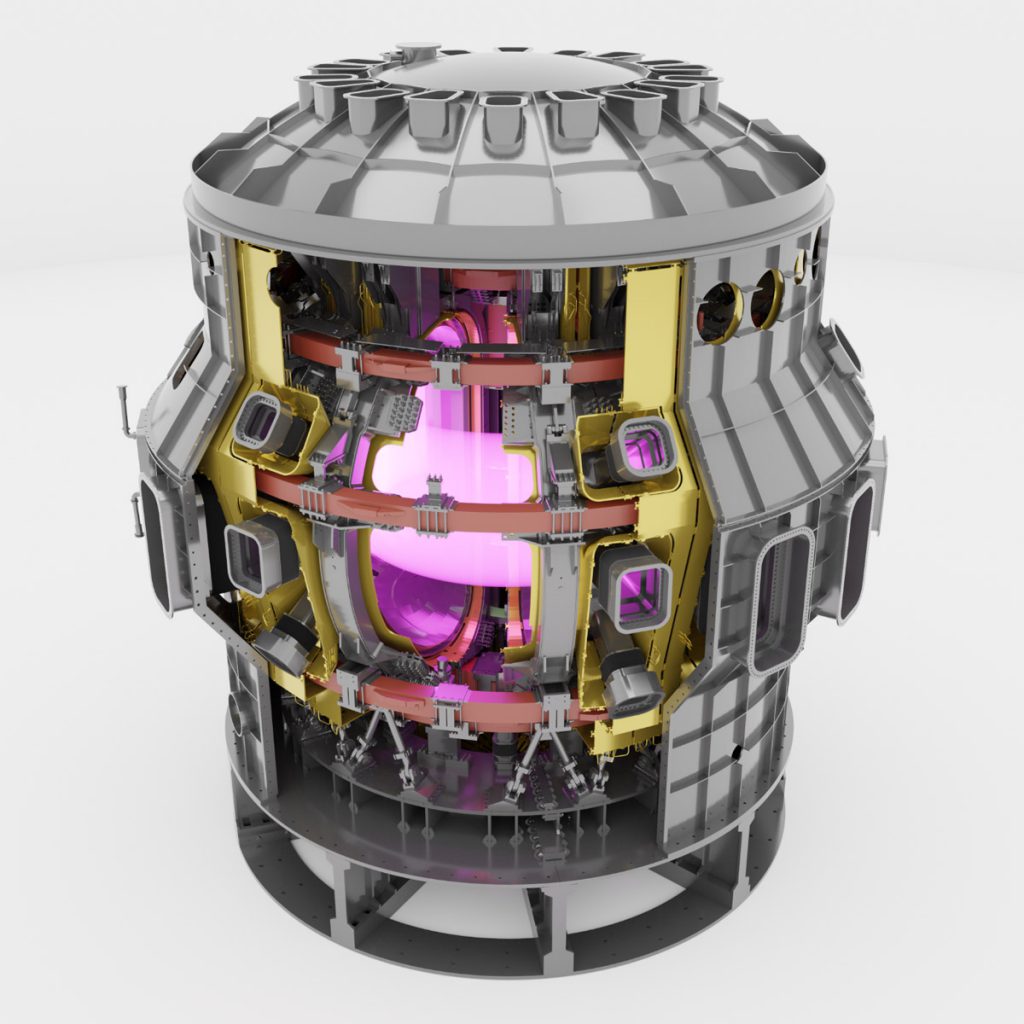
En parallèle, le CEA assure également la coordination technique du projet visant à développer (conception, qualification) le concept des cibles du futur divertor en tungstène de JT-60SA. Mehdi Firdaouss, ingénieur au CEA-IRFM est le « Lead Engineer » de ce projet. Pour répondre au besoin, des technologies innovantes (fabrication additive, matériau face au plasma à haute performance…) seront évaluées au regard de l’amélioration des performances (tenue en fatigue sous des flux thermiques supérieurs à 15 MW/m², tenue lors d’évènements énergétiques de l’ordre du GW/m² pendant quelques ms….). La fabrication additive permettrait par exemple de proposer une géométrie de composants avec une extraction de puissance très performante grâce une géométrie complexe des canaux de refroidissement.
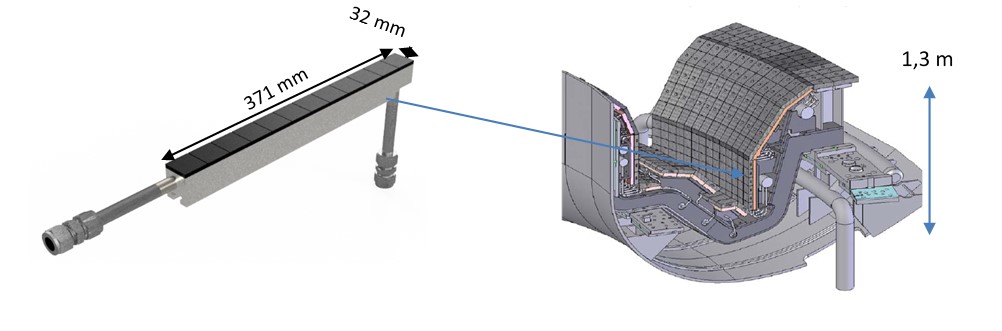