HADES (High heAt loaD tESt): a platform for qualifying components in the face of actively cooled plasma
The HADES platform offers an integrated environment for characterising and qualifying PFCs, the cornerstone of which is an electron beam gun for high-flux testing.
Given the need to test plasma-facing components and materials (PFC/PFM) and assembly technologies under high thermal flux for fusion applications, a new test bench based on an electron gun as the power source has been built at CEA-IRFM (France) between 2018 and 2020. The aim of this platform, called HADES (High heAt loaD tESt), is to assess the heat extraction capabilities of actively cooled PFCs exposed to high heat fluxes.
The facility can be used to study the operating range of actively cooled high-flux components (multilayer structures) in terms of thermal fatigue under cyclic thermal loading or boiling crisis (critical thermal flux), but also to estimate the thermal shock resistivity of PFMs.
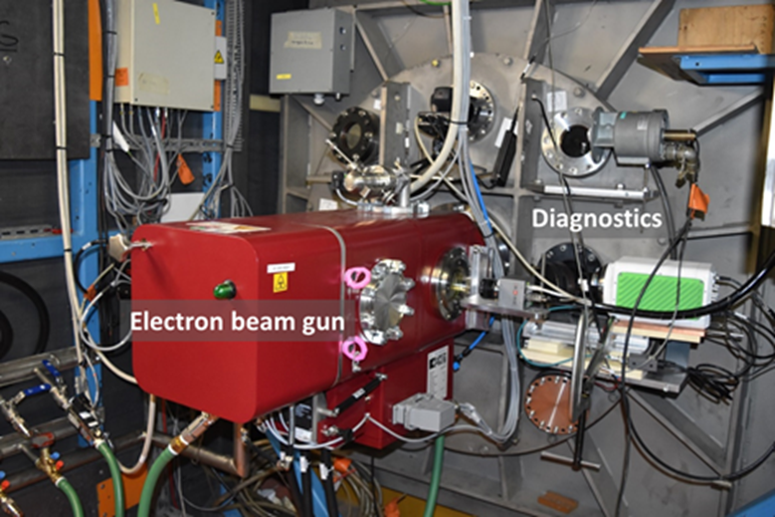
The HADES platform includes an electron beam (EB) with a maximum power of 150 kW (see Figure) operating at an accelerating voltage of 45 kV. The HADES electron gun can simulate steady-state experiments with a heat flux of several tens of MW/m² and transient events with a thermal energy of up to 1 GJ/m² for a few milliseconds.
A programmable scanning system allows several types of energy distribution (uniform or pitted), with a firing angle of ±25° with the normal to the surface.
The vacuum chamber (see Figure) is a parallelepipedic chamber with stainless steel walls ≥ 8mm thick. It has a large volume of around 8 m3 (the 2nd largest in Europe), and an opening 1.3 m in diameter, so it can accommodate components up to 1-2 m long. A mobile trolley holds the model or component to be tested and all the connections to the flexible cooling water loops. It slides on rails to introduce the model inside the enclosure and adjust the distance (1-2 m) between the model and the gun’s deflection point. A vacuum pumping system based on a diffusion pump (5000 l/s) combined with a roots pump and two primary pumps enables a pressure of ~10-5 hPa to be achieved.
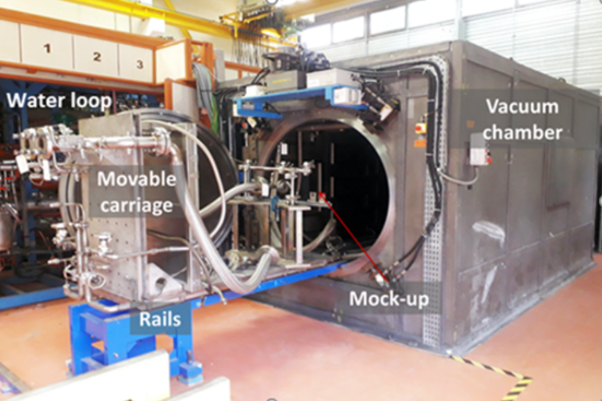
The component is connected to a cooling system (see Figure), which is a pressurised, superheated water loop, operating from 0.2 to 3.5 MPa, and at temperatures between 50°C and 220°C, with a maximum flow rate of 6 kg/s. This wide range of parameters gives the pressurised loop great flexibility.
Vacuum chamber and pressurised water loop
Six observation portholes are positioned around the opening of the gun for optical sighting and measurements. This set of diagnostics provides information on the calorimetric balance (absorbed heat flux), surface temperature up to 2300°C (infrared camera, pyrometers, pyro-reflectometer with remote positioning during tests), visual aspects or behaviour (CDD camera with remote focusing). The recording of stationary and transient surface temperature phenomena in real time makes it possible to study the thermal evolution of the components tested during thermal testing.
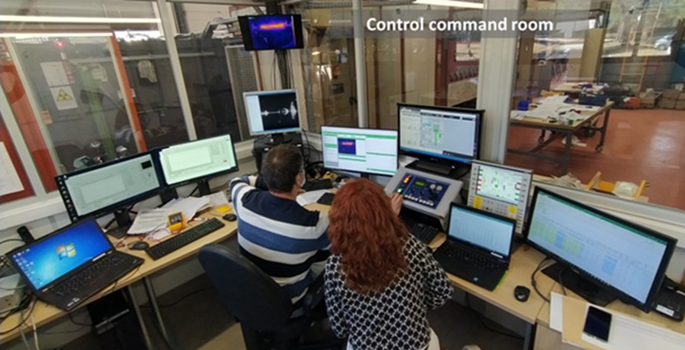