For the first time, an actively cooled model, with solid tungsten facing the plasma and Eurofer97 as a low-activation structural material, withstood heat fluxes of the order of 3 MW/m². The manufacture and testing of this model is the result of a project funded by the CEA’s transverse materials competence programme (DAM for powder spraying, DES/LITEN for hot isostatic compression and DRF/IRFM for the qualification of components against plasma).
The plasma-facing components of current fusion facilities such as WEST use tungsten assembled on a copper alloy. However, the resistance of copper to high neutron irradiation raises questions about the lifespan of these components in a future fusion power plant. Its replacement by a so-called low activation steel, Eurofer97, developed as part of the European fusion programme, is being studied.
Tungsten (W) is the preferred material for plasma in fusion power plants. Eurofer97, a low-activation martensitic steel, is being considered to replace copper as the structural material for first wall components and part of divertor 1 in future fusion power plants. These components are expected to be subjected to steady-state thermal loads of up to 1 MW/m², similar to those experienced by spacecraft during atmospheric re-entry. Currently, a tungsten coating of around 2 mm is the preferred technological solution (developed by the German institute KIT). The use of solid tungsten could offer the advantage of a dense material whose material characteristics are controlled before the component is completely manufactured. However, this approach requires an assembly solution between the tungsten and the Eurofer97.
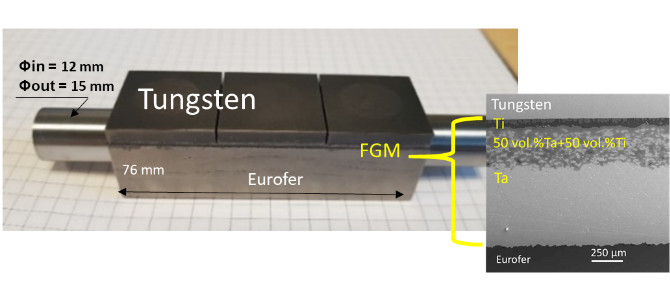
The first stage of this study focused on the choice of manufacturing technologies for the production of prototypes. Direct assembly of tungsten and Eurofer97 by hot isostatic pressing is not possible for metallurgical reasons [1]. The use of a gradient function material (FGM) between the tungsten and the Eurofer97 was chosen [2]. The composition of the interlayer between tungsten and Eurofer97 favours materials with reduced activation, which can be cold-sprayed and joined efficiently by diffusion bonding. For these reasons, the interlayer material is composed of titanium (Ti) and tantalum (Ta) function gradient materials. The advantages of the dynamic cold gas spraying process are that it provides materials with high density (>95%) and no oxidation within the deposit created. The final assembly between the tungsten (W), the Ti/Ta FGM material (900 µm ±150) and the Eurofer97 is achieved by hot isostatic pressing, followed by heat treatment to restore the mechanical properties of the Eurofer97.
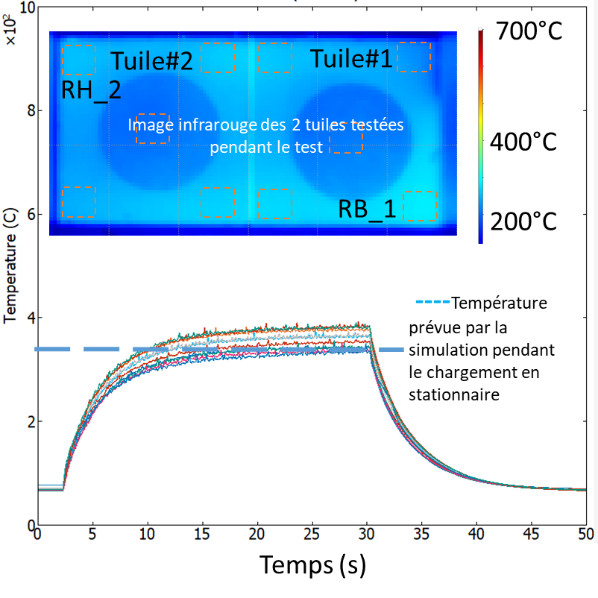
during tests at 1.15 MW/m².
The results of non-destructive testing (ultrasound, infrared thermography) show that a large part of the model produced has no defects. This part was therefore tested up to 3 MW/m² in the HADES high-flux test facility located at the IRFM. The thermal responses during the test revealed the good thermal behaviour of the model, since the experimental results were in line with those expected. No signs of tile failure were observed after the fatigue load of 120 cycles at 3 MW/m² (30 seconds loaded followed by 30 seconds unloaded). The tests will be continued until the component fails, in order to understand the damage mechanisms of such a technology. As Eurofer97 is a steel, the developments carried out for the assembly of tungsten to Eurofer97 could also be useful for the production of W assemblies on steel, which will be required for the first-generation components of the new ITER tungsten wall, part of the new 2024 baseline.
[1] M. Richou, I. Chu, G. Darut, R. Maestracci, M. Ramaniraka, and E. Meillot, “Titanium and Tantalum Used as Functional Gradient Interlayer to Join Tungsten and Eurofer97,” J. Nucl. Eng., vol. 3, no. 4, pp. 453–460, 2022, doi: 10.3390/jne3040031.
[2] M. Richou, “Performance assessment of thick W/Cu graded interlayer for DEMO divertor target,” Fusion Eng. Des., vol. 157, no. 111610, 2020.
1 Divertor: actively cooled component located at the bottom of the tokamak, which withstands the most intense heat flows.