The scientific and technical operation of tokamaks relies on a range of measurement or diagnostic systems. Among these, magnetic diagnostics occupy a special place, as they measure the plasma current and calculate its shape and position – essential data for plasma control. All magnetic sensors must be integrated into the vacuum chamber structure itself, so they are among the first measurement systems to be installed. CEA/IRFM has been involved in the development of these diagnostics for ITER, and has recently carried out measurement campaigns to qualify the sensors that will be installed in the ITER vacuum vessel. These measurement campaigns have been completed by tests of the associated electronics on the WEST tokamak.
CEA/IRFM has been involved in all phases of the development of ITER’s magnetic diagnostics, which include almost 2,000 sensors of 19 different types.
These include Mirnov coil-type sensors, compact LTCC (Low Temperature Co-fired Ceramic) sensors, hall probes, Rogowskis, fiber-optic current sensors, and more.
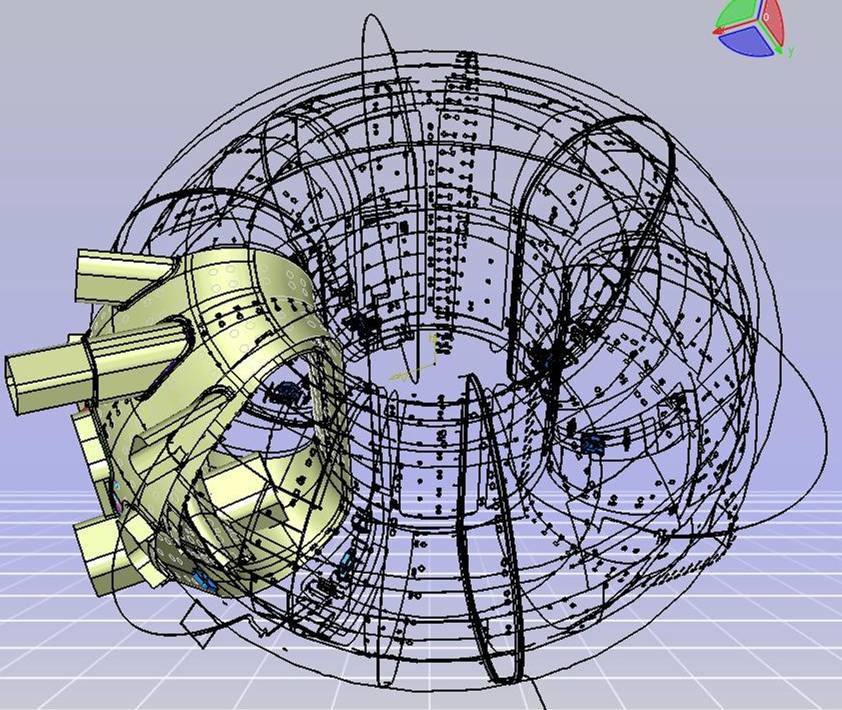
All these sensors are placed in a constrained environment in terms of geometry (some sensors are 40 m long and need to be flexible), available volume, temperature ranging from 4 to 500 Kelvin, radiation, particularly neutron fluxes and other factors. The work, carried out for the European domestic agency F4E (Fusion For Energy), involved selecting the right types of sensors, defining their configuration, and ensuring their integration within the tokamak itself, in the vacuum chamber and in the cryostat. Finally, a large number of qualification tests were carried out on prototype sensors.
Once this first phase was completed, the ITER sensors were manufactured by an industrial company. The CEA/IRFM was again contacted by the ITER Organization to qualify all the 450 sensors inside the vacuum vessel. The main task was to measure the frequency response of these sensors when subjected to magnetic fields with frequencies ranging from 20 Hz to 2 MHz, i.e. 5 orders of magnitude, which is considerable for a sensor. CEA/IRFM has developed a test bench for such measurements. Considering the number of sensors to be qualified and the number of measurements to be carried out, the test bench was fully automated via the implementation of control software. All this work has been carried out at CEA/IRFM over the last 2 years, and has generated a large database of results. These confirmed the conformity of each of the 450 sensors tested, including their sensitivity to a variable magnetic field.
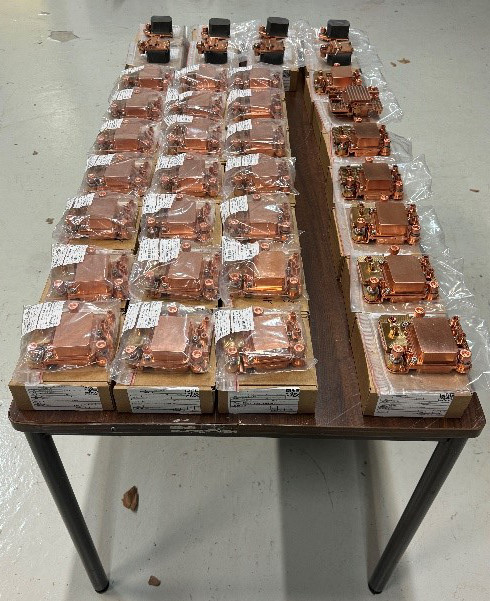
Magnetic inductive sensors, which measure only magnetic field variations, require special electronics to integrate the sensor signal (integrator board). These electronic boards must be developed and supplied by the European domestic agency (F4E). The qualification of their design includes a test on WEST in particular to check the stability of measurements on long duration plasmas.
Sample of ITER sensors
that have been calibrated
Such an integrator was connected to a sensor placed in the WEST vacuum chamber, and the data was recorded during 2 WEST experimental campaigns, i.e. almost 2,500 shocks representative of all the conditions that will be encountered on ITER: shocks of different durations, slow and rapid variations in the magnetic field, disruption, etc. These tests validated the quality of the ITER integrators under all circumstances. These tests validated the quality of ITER integrators in all circumstances.
The extension of these tests on WEST is under discussion, as is CEA/IRFM’s participation in the development of integrators for the KSTAR tokamak in Korea.