IRFM designed, manufactured and qualified some mock-ups for DEMO divertor developped in a EUROfusion project. These components use an innovative material which resisted up to 25 MW/m2 heat fluxes.
In order to meet the extreme conditions experienced by the divertor of the DEMO reactor in terms of high heat flux (10 MW / m² stationary and 20 MW / m² transient) and neutronic flux (<10 dpa), several design options and materials are envisaged for this component. In the WP-DIV Eurofusion project, since 2014, different concepts are compared with the reference concept “ITER-LIKE” developed by ENEA. These concepts (developed by KIT, IPP, CCFE and CEA (IRFM)) mainly use tungsten as armor material and CuCrZr as structural material. These concepts seek to improve the bond between the armor and structural material which will have to withstand important thermomechanical stresses.
Thus, by substituting the copper interlayer (which is the case for the reference concept) with a Functionally Gradient Material (FGM), the concept developed by CEA (IRFM) aims at obtaining a gradual transition of the thermomechanical properties between the W and the CuCrZr, making it possible theoretically to improve the mechanical strength of the bond.
To manufacture such mock-ups with FGM interlayer, different tasks were carried out:
- Optimization of the thermomechanical behaviour through finite element modeling. Therefore, an optimized design was defined in 2015.
- In 2016, functionally graded material was manufactured by physical vapor deposition (deposit inside the tungsten tiles). This deposit, of thickness ~ 25 μm, was realized by the french company DEPHIS.
- Hot isostatic pressing was performed in order to bond the tiles with the CuCrZr tube. 6 mock-ups, each consisting of 10 tiles, were assembled using this method in March 2016 at the CEA / DRT /LITEN.
- Non-destructive tests were performed with ultrasonic (ENEA) and infrared thermography (SATIR device – CEA / IRFM) methods on the 6 manufactured mock-ups. This allowed showing a global good quality of the bonding at the end of the assembly step. Only 3 Monoblocks out of 60 (5%) have thermal imperfections probably attributed to a defect at the interface or tungsten itself.
- Finally, high heat flux tests (IPP Garching) have shown (at the end of October 2016) that these mock-ups can withstand without detectable damage (i.e. without cracking or delamination of the interface) each of the steps defined by the WPDIV test program: 3 mock-ups have undergone progressive thermal loading of up to 15 MW / m². Then 2 of these models underwent 100 cycles to 10 MW / m² while the third model underwent 100 cycles to 15 MW / m². The three models then underwent progressive thermal loading up to 25 MW / m² (5 cycles): no damage had been observed, one of these models underwent 100 cycles at 20 MW / m².
Such levels of performance are promising and will be consolidated by a second high heat flux testing campaign as well as metallographic inspections in 2017!
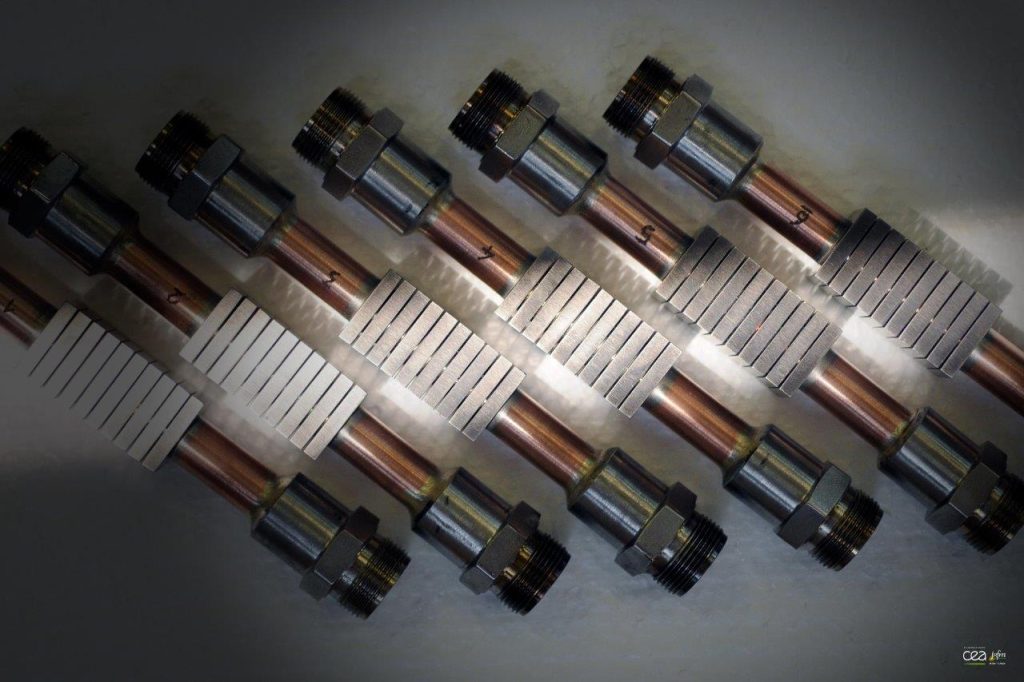