The first of the 18 JT-60SA Toroïdal Field coil was delivered at CEA Saclay on December 17th 2015. There, it will be tested before to be shipped to Japan. This coil, manufactured by Alstom/General Electric at Belfort France under CEA responsibility, is the largest ever built.
“We did it!” That is what Patrick Decool, JT-60SA Toroidal Field Coil Project Leader at CEA, said with a big smile and a great feeling of satisfaction when the truck loaded with the first TF coil left the Alstom/GE factory at Belfort on the sunny morning of the 15th of December 2015. And so were undoubtedly thinking the members of the Alstom/GE team led by Marc Nusbaum and Gérard Billotte, the members of the CEA team led by Patrick and the members of the F4E and ENEA teams who have worked hard throughout the last few years to reach this important milestone.
The TF Coils are one of the key components for the scientific success of any Tokamak. To appreciate the challenges that have been overcome thus far it is enough to know that these superconducting coils for JT-60SA are among the largest in the world in size, shape and magnetic characteristics. For fusion devices they will only be overshadowed by the ITER TF Coils.
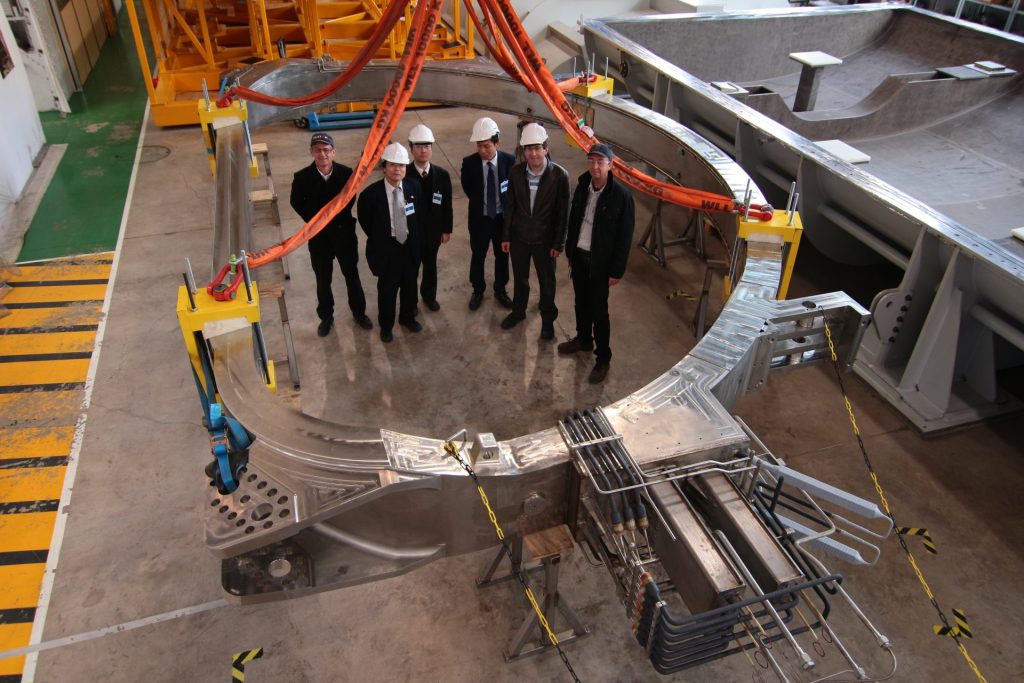
The design and manufacturing of the JT-60SA TF Coils are the outstanding results of an intense, fruitful and efficient international collaboration. The design activities during the years 2007-2011 were widely shared between European and Japan Institutions: JAEA, F4E, ENEA and CEA. The manufacturing and testing of the TF coils, defined as European contributions to JT-60SA in the framework of the Broader Approach Agreement, were split in several lots, each requiring a high level of skill and quality.
F4E procured the superconducting strands manufactured by the Furukawa Company in Japan and their subsequent cabling and jacketing to produce Cable-In-Conduit conductor by the Italian consortium ICAS. ENEA procured the TF coil casings manufactured by the Walter Tosto Company.
Using these components, CEA and ENEA, who each have the duty to produce, with a high level of accuracy and reliability, nine coils plus one spare, have placed industrial contracts with renowned superconducting coil manufacturers: Alstom/GE for CEA and ASG for ENEA.
The industrial contracts include: the winding of the conductors into six double pancakes per coil, the electrical joints and terminals for power supply, the resin impregnation of the winding pack, which provides it with the necessary electrical insulation and mechanical integrity , the insertion of the winding pack into the casing and the closure welding of the casing, the embedding impregnation of the winding pack within the casing, the final machining of the integrated coil and the fitting of the final cooling pipes and measuring sensors. At each step the manufacturer has to complete a dedicated testing and quality control program.
Before the start of the manufacturing each manufacturer had to develop and qualify the manufacturing process and manufacturing tools.
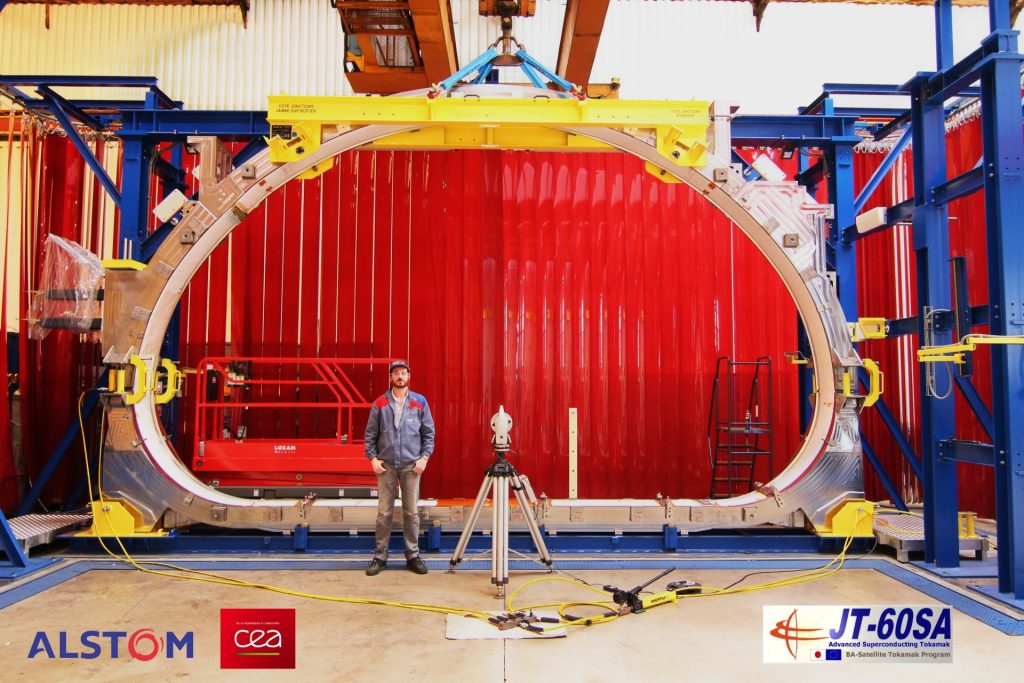
For the CEA coils, the winding operations for the first coil started in January 2014 and its completion was achieved in December 2015 (fig.3). Now at Belfort in the General Electric (former Alstom) premises eight TF coils are in work at different manufacturing steps along the production line. They will all be delivered, at a regular rate, by mid-2017.
The 17th of December, the first coil was delivered at the Cold Test Facility at CEA Saclay, where it will be tested at its nominal operating conditions (25.7kA, 4.5K) as well as being subject to a temperature-induced quench. Then it will be assembled with its Outer Intercoil Structures, re-packed and transported to Japan. The 17 remaining coils, and the two spare coils, will all experience similar full current testing in Saclay before shipment to Naka.